Your solar project’s success depends on one critical component. Without reliable MC4 connectors, your entire solar system becomes vulnerable to weather damage and electrical failures.
The right MC4 solar connector manufacturer determines your project’s 25-year performance. Quality connectors prevent costly system failures, ensure safety compliance, and maximize energy production through weatherproof connections that last decades.
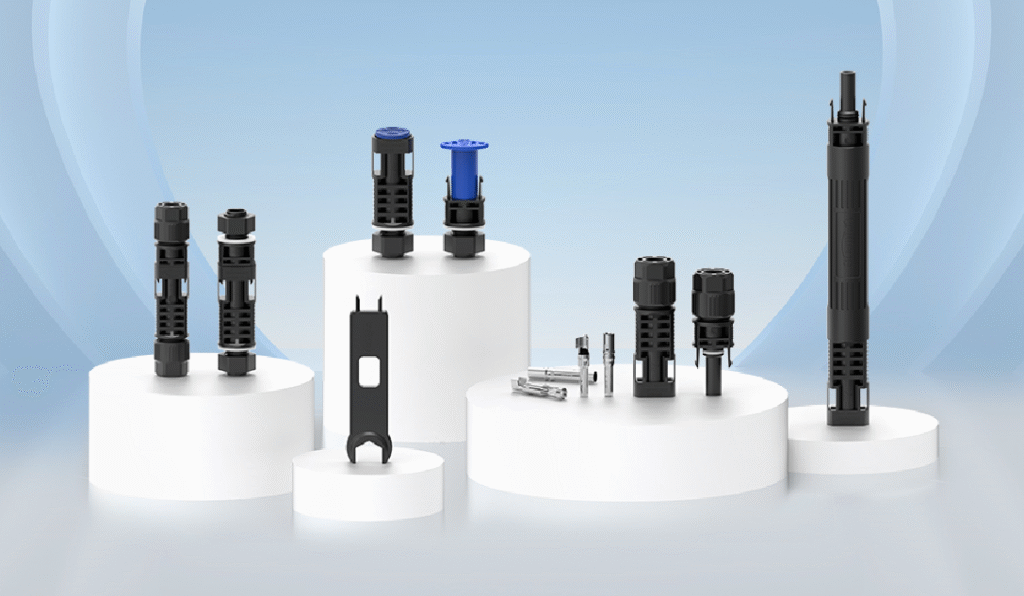
I learned this lesson the hard way when a client’s solar installation failed after just two years. The cheap connectors corroded, causing dangerous arcing and system shutdown. This experience taught me the critical importance of connector quality evaluation.
That’s why I created this comprehensive guide to help you select the right MC4 solar connector manufacturer. This guide provides you with practical evaluation criteria, quality assessment methods, and cost-benefit analysis tools. You’ll learn how to identify reliable suppliers, avoid costly mistakes, and ensure long-term project success.
In the following sections, I’ll analyze the critical role of MC4 connectors in solar system performance, share proven methods for identifying reliable manufacturers, explain essential manufacturing processes that ensure quality, discuss the importance of international certifications for market acceptance, and compare manufacturing locations to help you make informed sourcing decisions. These insights will help you avoid the expensive mistakes that cost my client thousands in system repairs and downtime.
What Makes MC4 Connectors Critical for Solar Systems?
Poor connector quality creates expensive problems. System failures, safety hazards, and warranty claims follow when manufacturers cut corners on materials or testing.
MC4 connectors create the essential electrical pathway between solar panels and inverters. They must withstand extreme temperatures, UV radiation, moisture, and mechanical stress while maintaining perfect electrical contact for 25+ years.
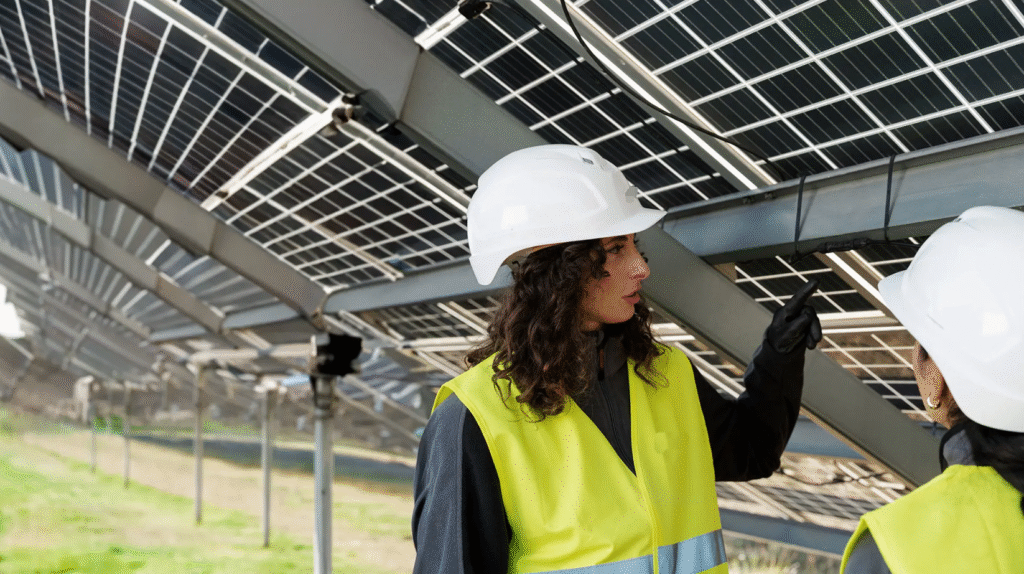
The name “MC4” comes from Multi-Contact (the original manufacturer) and “4” for the 4mm conductor size. These specialized connectors lock together to create weatherproof connections. The male and female components form a secure bond that prevents water ingress and maintains electrical integrity.
Modern solar installations require connectors that handle high DC voltages (1000V-1500V) while providing IP67/IP68 waterproof protection. The connector housing uses UV-resistant polymers like PPO or PA66 that won’t degrade under constant sunlight. Inside, precision-stamped copper contacts with tin or silver plating ensure low resistance and prevent corrosion.
Component | Material | Function |
---|---|---|
Housing | PPO/PA66 | UV protection, structural integrity |
Contacts | Tin-plated copper | Electrical conductivity |
Seals | EPDM rubber | Waterproof protection |
Locking ring | Stainless steel | Secure connection |
Temperature cycling from -40°C to +90°C tests connector durability. Quality manufacturers subject every batch to accelerated aging that simulates decades of outdoor exposure. Pull-out testing exceeds 120N force to verify mechanical strength.
How Do You Identify a Reliable MC4 Solar Connector Manufacturer?
Manufacturing quality varies dramatically between suppliers. Some manufacturers prioritize cost over performance, leading to field failures that damage entire projects.
Look for manufacturers with TÜV, UL, and CE certifications, advanced injection molding equipment, automated assembly lines, and comprehensive testing protocols that exceed industry standards.
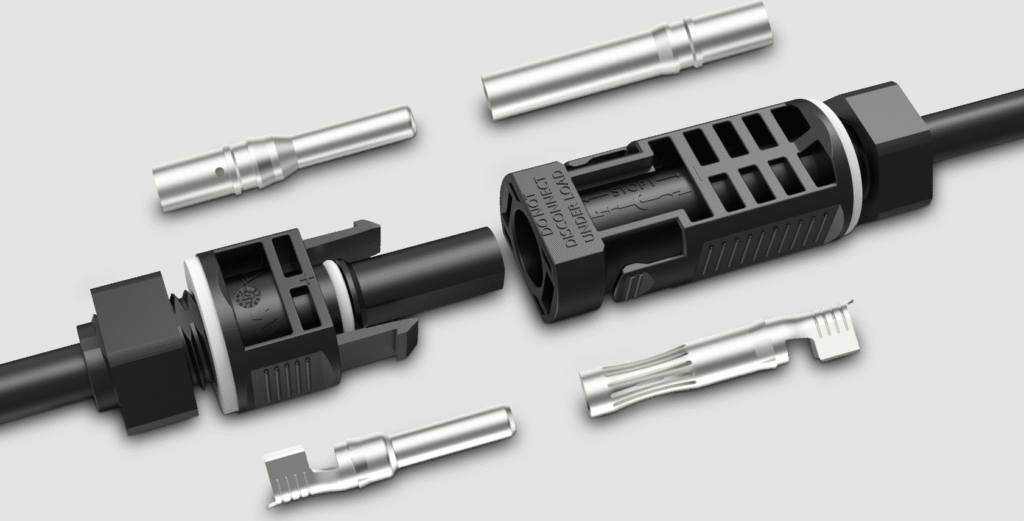
At AGX, we invested in servo-driven injection molding machines with precise temperature and pressure control. Our engineering team uses computer-aided design software like CREO for mold design and simulation tools to predict defects before production starts.
Raw material selection separates quality manufacturers from budget suppliers. Premium housing materials include high-performance PPO with exceptional UV resistance and flame-retardant properties. The metal contacts use high-conductivity copper with precision plating processes. EPDM rubber gaskets provide superior weathering resistance compared to cheaper alternatives.
Quality control starts with incoming material inspection and continues through every production stage. Automated optical inspection systems check dimensional accuracy and surface finish. Electrical testing verifies contact resistance below 0.5 milliohms and high voltage performance at 6kV for one minute.
Testing Parameter | Standard Requirement | Quality Manufacturer |
---|---|---|
Pull-out force | 60N minimum | 120N+ actual |
Contact resistance | <2.5 milliohms | <0.5 milliohms |
Voltage rating | 1000V DC | 1500V DC |
Temperature range | -40°C to +85°C | -40°C to +90°C |
Production capacity indicates manufacturer stability and scalability. Established manufacturers produce 10,000-20,000 connector sets daily using multiple production lines. This volume allows for consistent quality control and competitive pricing.
What Manufacturing Processes Ensure MC4 Connector Quality?
The manufacturing process directly impacts connector performance and lifespan—shortcuts in production lead to premature failures that cost thousands in replacement and repair.
Advanced injection molding, precision metal stamping, automated assembly, and comprehensive testing create MC4 connectors that perform reliably for 25+ years in harsh outdoor environments.
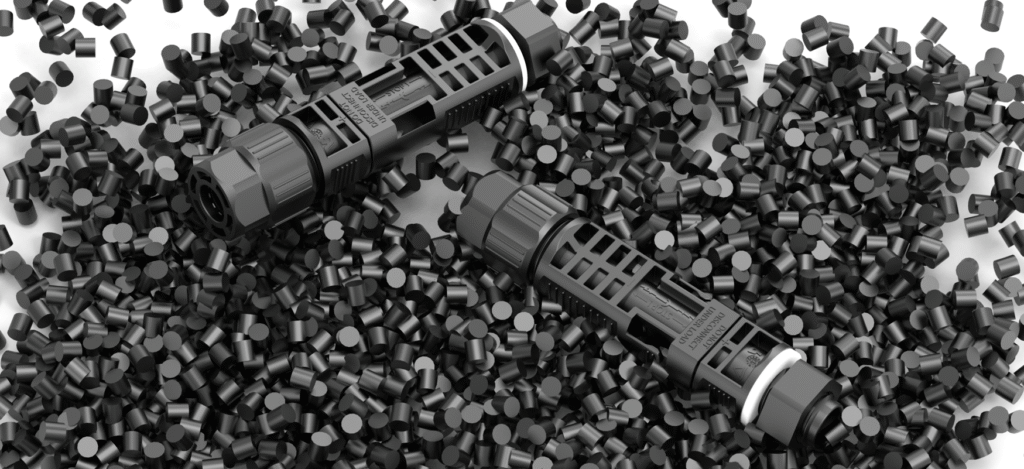
Our manufacturing process at AGX demonstrates the importance of each production step. Injection molding requires precise temperature control and pressure management to achieve dimensional accuracy. Multi-cavity molds enable high-volume production while maintaining quality consistency. Every molding machine has dedicated inspectors who perform a 100% visual inspection.
Metal contact production uses computer-controlled stamping and forming with tight tolerances. Progressive die technology ensures efficient production while maintaining precision. The plating process applies a uniform tin or silver coating to enhance conductivity and prevent corrosion. Dimensional and electrical testing verify that every contact meets specifications.
Assembly automation eliminates human error and ensures consistent quality—servo-controlled machines position components with precision. Automated equipment handles critical processes like stop ring crimping. Digital image detection and laser systems provide 100% inspection coverage.
Environmental testing validates long-term performance. Temperature cycling from -40°C to +90°C simulates seasonal variations. UV exposure testing uses accelerated aging chambers that compress decades of sunlight into weeks. Salt spray testing verifies corrosion resistance in coastal environments.
Process Stage | Quality Control | Equipment |
---|---|---|
Injection molding | Visual inspection, dimensional check | Servo-driven machines |
Metal stamping | Electrical testing, plating verification | Progressive dies |
Assembly | Automated positioning, force monitoring | Servo-controlled systems |
Testing | Environmental simulation, pull testing | Climate chambers |
Certification testing by independent laboratories confirms compliance with international standards. TÜV certification validates electrical safety and performance. UL listing ensures North American market acceptance. CE marking confirms European regulatory compliance.
Why Do International Certifications Matter for MC4 Connectors?
Certifications validate manufacturer quality and enable global market access. Products without proper certifications face regulatory rejection and liability issues.
TÜV, UL, and CE certifications ensure MC4 connectors meet international safety standards, providing legal protection and market acceptance for solar installations worldwide.
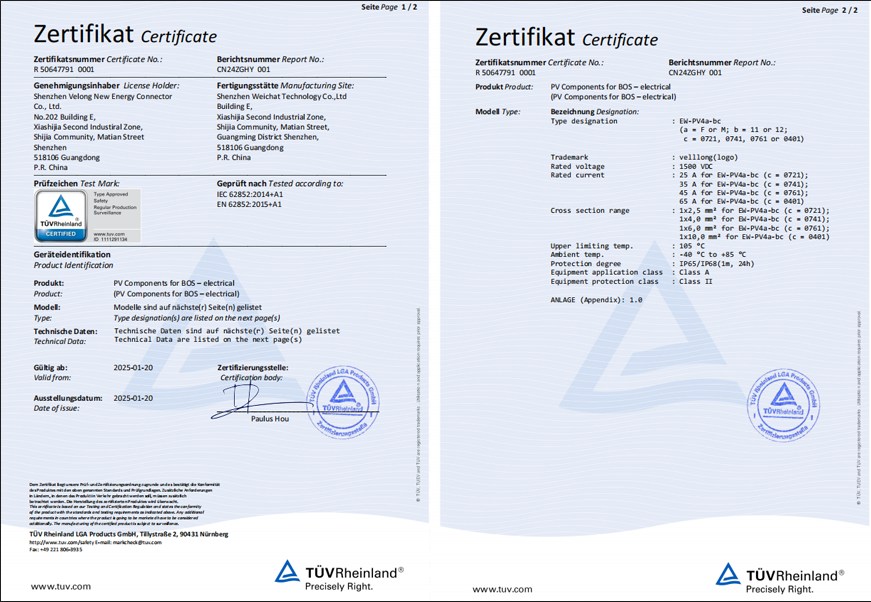
I learned about certification importance when a client’s project was rejected by local authorities. The connectors lacked proper certifications, requiring expensive replacement with certified alternatives. This delay cost thousands in project delays and material waste.
TÜV certification validates electrical safety through comprehensive testing. High voltage testing at 6kV for one minute ensures insulation integrity. Contact resistance measurements verify electrical performance. Temperature cycling and humidity testing validate environmental durability.
UL listing enables North American market access through rigorous safety evaluation. Fire resistance testing ensures materials won’t propagate flames. Mechanical testing validates connector strength and durability. Environmental testing confirms performance across temperature and humidity ranges.
CE marking demonstrates European regulatory compliance through harmonized standards. EMC testing validates electromagnetic compatibility. RoHS compliance ensures environmental safety through restricted substance limits. REACH compliance addresses chemical safety concerns.
Certification | Testing Requirements | Market Access |
---|---|---|
TÜV | High voltage, temperature, humidity | Global acceptance |
UL | Fire resistance, mechanical strength | North America |
CE | EMC, RoHS, REACH | European Union |
ISO 9001 | Quality management systems | Process validation |
Quality manufacturers maintain multiple certifications to serve global markets. They invest in testing equipment and maintain relationships with certification bodies. Regular audits ensure ongoing compliance with evolving standards.
How Does Manufacturing Location Impact MC4 Connector Quality?
Geographic location affects manufacturing capabilities, cost structure, and supply chain efficiency. Some regions excel in precision manufacturing while others focus on cost reduction.
China leads global MC4 connector manufacturing through advanced automation, skilled workforce, integrated supply chains, and continuous technology investment that delivers quality products at competitive prices.
My supply chain experience shows China’s unique advantages in connector manufacturing. The concentration of solar panel production creates an integrated ecosystem where connector manufacturers work closely with panel producers. This proximity enables rapid feedback and continuous improvement.
Chinese manufacturers invest heavily in advanced automation and production technologies. State-of-the-art injection molding machines, automated assembly lines, and computerized testing equipment match or exceed global standards. The technical expertise developed through high-volume production benefits all customers.
Scale advantages enable cost efficiencies without compromising quality. Large production runs reduce per-unit costs through material purchasing power and manufacturing efficiency. This scale also supports investment in quality control equipment and skilled personnel.
Global compliance knowledge comes from serving international markets. Chinese manufacturers understand diverse regulatory requirements and maintain multiple certifications. They adapt products for different market needs while maintaining core quality standards.
Manufacturing Advantage | Benefit | Impact |
---|---|---|
Integrated supply chain | Faster development cycles | Reduced costs |
Advanced automation | Consistent quality | Higher reliability |
Technical expertise | Specialized knowledge | Better performance |
Global compliance | Market access | Wider adoption |
Value engineering balances performance and cost through continuous improvement. Manufacturers optimize designs for better performance while reducing material usage. They identify cost savings opportunities without compromising quality or durability.
Conclusion
This comprehensive guide provides you with the essential knowledge to select reliable MC4 solar connector manufacturers and avoid costly project failures. Understanding connector criticality, manufacturer evaluation criteria, quality manufacturing processes, certification requirements, and location advantages helps you make informed decisions that protect your solar investments and ensure long-term performance success.