Water damage costs businesses millions every year. Electrical failures happen when moisture gets into connections. I’ve seen too many projects fail because of this simple problem.
Waterproof connectors are sealed electrical components that prevent water and moisture from entering connection points. They protect electrical circuits in wet environments and ensure reliable performance in harsh conditions.
So I put together this complete guide to help you better evaluate and find the right waterproof connectors for your needs. This guide provides real value in three key areas: saving project costs, avoiding system failures, and choosing the optimal solution for your specific application.
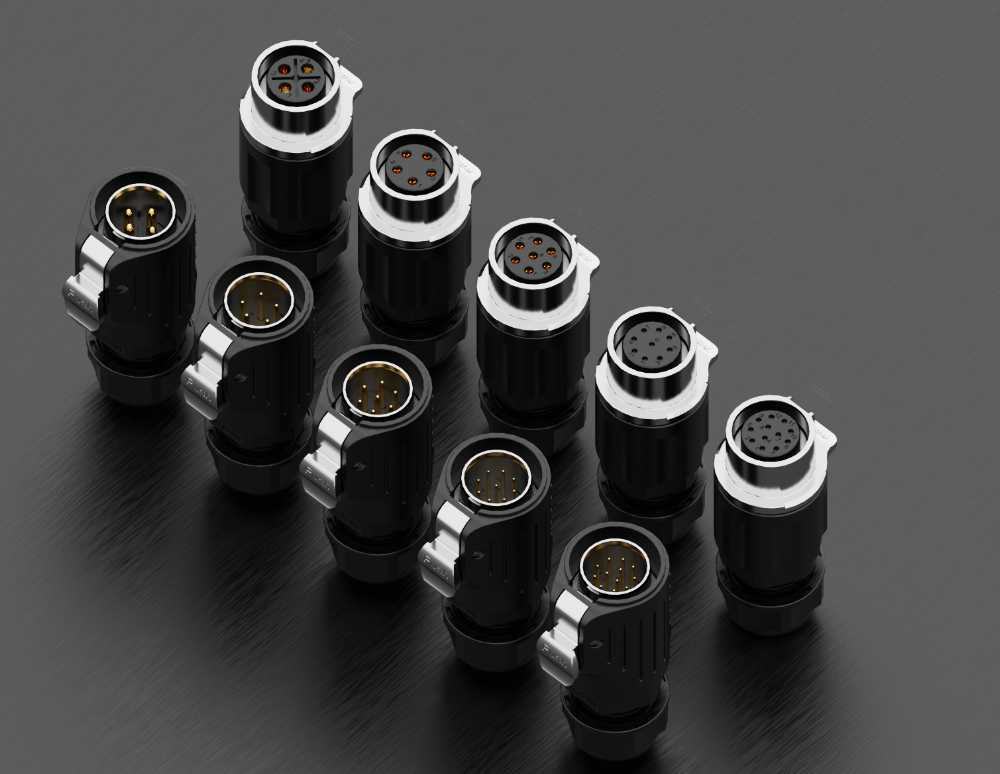
After 15 years in the waterproof connector industry, I’ve learned that understanding these components can save you time, money, and headaches. Let me share what I’ve discovered about waterproof connectors and why they matter for your projects.
In this comprehensive guide, I’ll walk you through the essential knowledge you need to make smart connector decisions. First, I’ll explain what makes a connector truly waterproof by breaking down the design features and materials that provide real protection. Then I’ll show you where waterproof connectors deliver value so you can avoid unnecessary costs while ensuring protection where it matters. Next, I’ll guide you through choosing the right waterproof connector by matching technical specifications to your specific requirements. Finally, I’ll reveal the most common installation mistakes that cause failures so you can avoid these costly problems from the start.
What Makes a Connector Truly Waterproof?
Most people think any sealed connector is waterproof. This mistake cost them later. True waterproof protection requires specific design features.
Waterproof connectors use rubber seals, gaskets, and special materials to create airtight barriers. They meet IP67 or IP68 ratings, which means they can handle water submersion without damage.
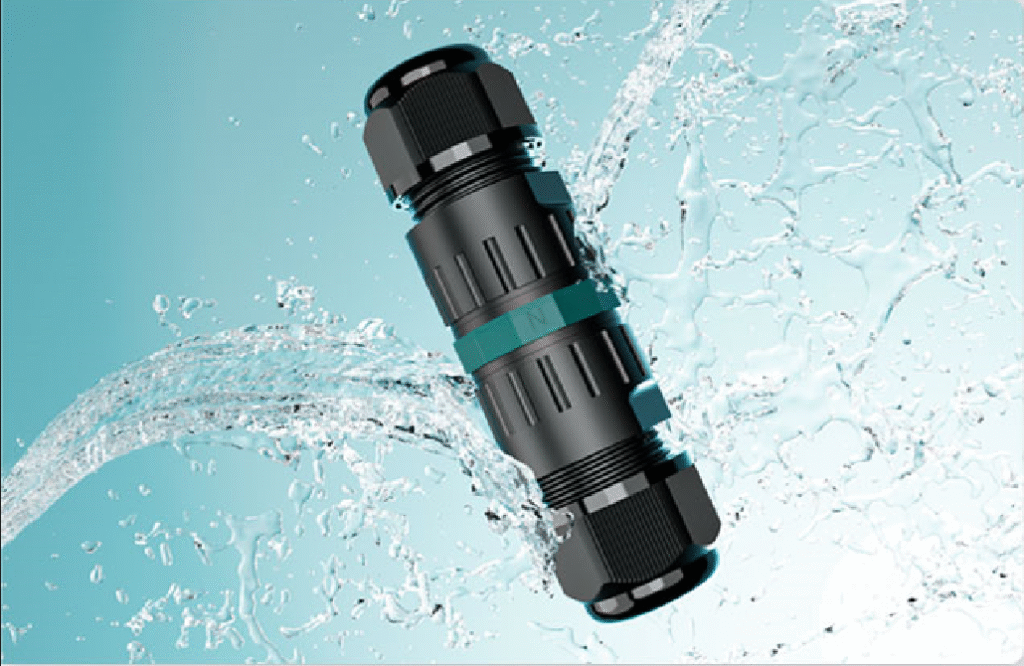
The key difference lies in the sealing system. I’ve tested hundreds of connectors over the years. The best ones use multiple sealing layers. First, there’s the main housing seal that wraps around the entire connector body. The individual wire seals protect each connection point. Finally, a locking mechanism ensures the seal stays tight under pressure.
Material choice matters too. Standard rubber breaks down in saltwater or extreme temperatures. Quality waterproof connectors use silicone or EPDM rubber that handles these conditions. The housing material also affects performance. Stainless steel works best for marine applications. Plastic housings work fine for indoor wet areas like bathrooms.
Component | Standard Grade | Marine Grade | Industrial Grade |
---|---|---|---|
Housing | Plastic/Nylon | Stainless Steel | Aluminum Alloy |
Seals | Basic Rubber | Silicone/EPDM | Fluorocarbon |
Contacts | Brass | Tinned Copper | Gold Plated |
IP Rating | IP65 | IP68 | IP67 |
Where Do You Need Waterproof Connectors?
Many people buy waterproof connectors for the wrong applications. Others skip them when they really need protection. Location and environment determine your needs.
Waterproof connectors are essential for outdoor lighting, marine equipment, automotive systems, and industrial machinery exposed to moisture. They prevent corrosion and electrical failures in wet conditions.
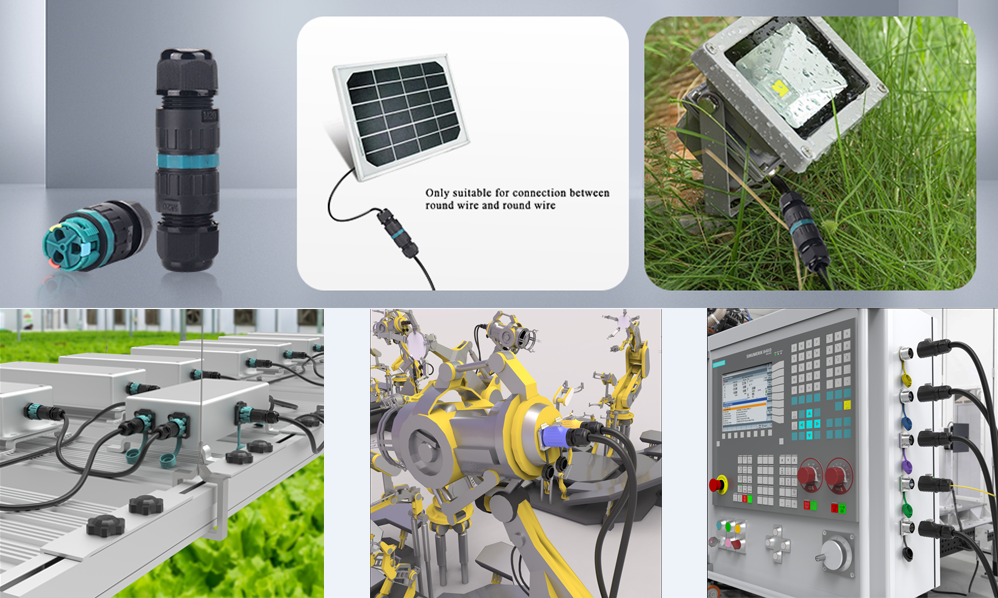
Marine applications represent the toughest environment. Saltwater corrodes everything it touches. I remember working with a yacht manufacturer who kept having electrical problems. Their regular connectors failed within months. We switched to marine-grade waterproof connectors with stainless steel housings. The problems disappeared.
Automotive systems face different challenges. Road salt, car washes, and engine heat create harsh conditions. Modern cars use waterproof connectors for engine management systems, lighting, and sensors. Electric vehicles need even more protection because water and high voltage don’t mix.
Industrial settings vary widely. Food processing plants need connectors that handle washdown procedures. Chemical plants require protection against corrosive vapors. Outdoor security cameras need connectors that work in all weather conditions.
Application | Key Challenges | Recommended IP Rating | Special Features |
---|---|---|---|
Marine | Salt corrosion, submersion | IP68 | Stainless steel housing |
Automotive | Vibration, temperature, chemicals | IP67 | Locking mechanisms |
Industrial | Pressure washing, chemicals | IP65-IP67 | Chemical resistant seals |
Outdoor | Weather, UV exposure | IP65 | UV resistant materials |
How Do You Choose the Right Waterproof Connector?
Picking the wrong connector wastes money and creates problems later. I’ve seen projects delayed because someone chose based on price alone. Smart selection starts with understanding your specific needs.
Choose waterproof connectors based on current rating, voltage requirements, environmental conditions, and connection type. Match the IP rating to your application and consider future maintenance needs.
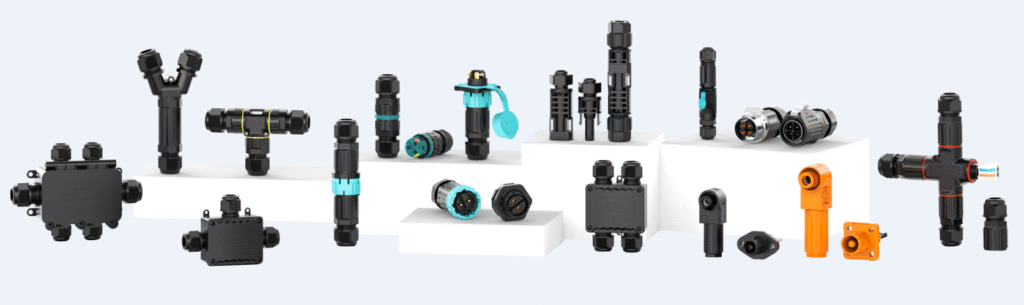
Current capacity comes first. Undersized connectors overheat and fail. I always recommend checking the actual current draw, not just the rated capacity of your equipment. Add a 20% safety margin for good measure. Temperature affects current capacity, too. Connectors rated for 10 amps at room temperature might only handle 8 amps at 60°C.
Voltage rating seems straightforward, but creates confusion. DC and AC voltages behave differently. High-frequency signals need special consideration. Automotive 12V systems look simple, but starter motors create voltage spikes that can damage poorly designed connectors.
Environmental factors matter more than people realize. Temperature cycling causes expansion and contraction. This movement can break seals over time. Vibration loosens connections. Chemical exposure degrades materials. UV light makes plastic brittle.
Connection method affects reliability and maintenance. Solder connections provide the best electrical performance but can’t be easily serviced. Screw terminals allow field repairs but need periodic tightening. Push-in connectors work fast but may not hold up under vibration.
Factor | Consideration | Impact on Selection |
---|---|---|
Current | Actual load + 20% margin | Determines contact size |
Voltage | DC/AC, frequency, spikes | Affects insulation needs |
Temperature | Operating range, cycling | Influences material choice |
Vibration | Frequency, amplitude | Requires locking features |
Chemicals | Type, concentration | Determines seal material |
Maintenance | Access, frequency | Affects connection type |
What Are the Most Common Installation Mistakes?
Perfect connectors fail because of poor installation. I’ve troubleshot thousands of connection problems. Most failures trace back to these basic mistakes.
Common installation errors include insufficient wire preparation, overtightening, wrong tools, and skipping the seal check. Proper installation requires following the manufacturer’s specifications and using correct techniques.
Wire preparation creates the foundation for reliable connections. I see people strip too much insulation, leaving exposed copper that corrodes. Others strip too little, creating poor contact. The correct strip length depends on your connector type. Circular connectors need precise measurements. Rectangular connectors offer more flexibility.
Overtightening damages seals and threads. Undertightening allows water entry. Most connectors specify torque values. Use a torque wrench for critical applications. Hand tightening works for many connectors but requires experience to get right.
Tool selection matters more than people think. Wrong tools damage contacts and housings. Crimping tools must match your connector type. Generic tools create inconsistent connections. Quality tools cost more upfront but save money through better reliability.
Seal inspection gets skipped under time pressure. This shortcut causes most field failures. Check every seal before final assembly. Look for cuts, stretching, or contamination. Replace questionable seals rather than hoping they’ll work.
Environmental preparation affects long-term performance. Clean all surfaces before assembly. Remove oil, dirt, and corrosion. Apply appropriate sealants where specified. Allow proper cure time before service.
Mistake | Consequence | Prevention |
---|---|---|
Wrong strip length | Poor contact, corrosion | Use strip gauge |
Overtightening | Damaged seals, cracked housing | Follow torque specs |
Generic tools | Inconsistent connections | Use proper crimping tools |
Skipped seal check | Water entry, failures | Inspect every seal |
Dirty surfaces | Poor sealing, corrosion | Clean before assembly |
Rushed assembly | Multiple problems | Allow proper time |
Why AGX Connector Solutions Stand Out?
Throughout my 15 years in this industry, I’ve tested countless waterproof connectors from different manufacturers. Many promise waterproof protection but fail when it matters most. This experience led me to create AGX Connector with a clear mission: making electrical connections safer and more convenient.
AGX Connector products deliver proven waterproof performance through rigorous testing, premium materials, and real-world application experience. We understand what works because we’ve seen what fails.
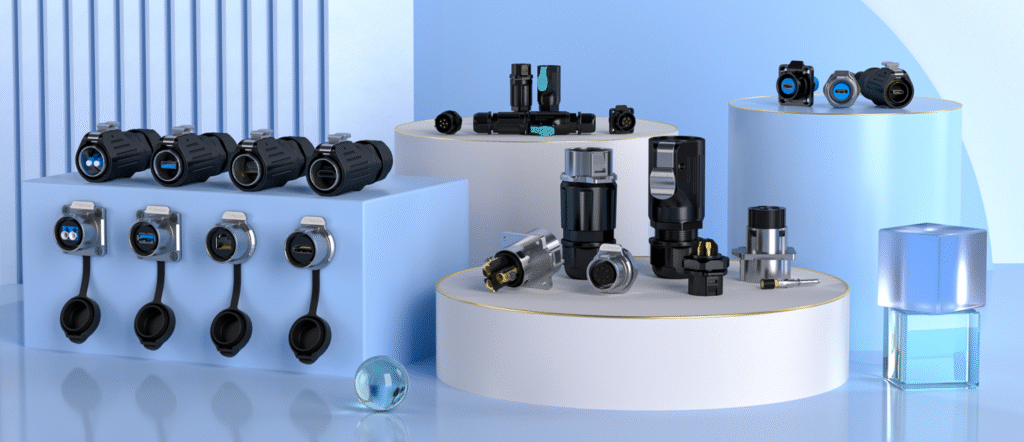
What sets AGX Connector apart starts with our testing standards. Every connector goes through submersion tests, temperature cycling, and vibration testing that exceed industry requirements. I’ve personally overseen these tests because I know the cost of field failures. We use marine-grade materials even for standard applications because durability matters more than cutting costs.
Our product line covers the applications I’ve discussed in this guide. Marine connectors with stainless steel housings for saltwater environments. Automotive connectors that handle engine heat and road chemicals. Industrial connectors are rated for pressure washing and chemical exposure. Each product solves specific problems I’ve encountered over the years.
Technical support makes the difference when you need help. Our team understands real-world applications because we’ve been there. We can help you select the right connector, avoid installation mistakes, and troubleshoot problems. This knowledge comes from years of solving connector challenges across different industries.
Quality control ensures consistent performance. We inspect every batch and track performance data from customer applications. This feedback loop helps us improve products and catch issues before they reach customers. It’s the approach I wish more manufacturers would take.
AGX Advantage | Standard Approach | AGX Approach |
---|---|---|
Testing | Basic IP rating | Exceed standards |
Materials | Cost optimization | Performance first |
Support | Generic advice | Application expertise |
Quality | Batch sampling | 100% inspection |
Conclusion
This comprehensive guide provides the knowledge you need to select, install, and maintain waterproof connectors effectively. Understanding what makes connectors truly waterproof, identifying where protection matters most, choosing the right specifications, and avoiding installation mistakes will save you time, money, and project delays. With proper waterproof connectors and correct installation, you can eliminate moisture-related electrical failures and ensure reliable system performance in any environment.